Safety isn't just a precaution in the work-at-height world of zip lines, adventure parks, and challenge courses; it's a mandate. The Occupational Safety and Health Administration (OSHA) sets and enforces standards to support workplace safety. One of its key directives pertains to the equipment used by work-at-height employees, including those working at canopy tours, adventure parks, challenge courses, and similar facilities.
OSHA's standards recognize that the quality and reliability of equipment play a pivotal role in worker safety. ANSI-rated equipment has undergone stringent testing for scenarios such as sudden drops, weight loads, and extreme environmental conditions – exactly the situations work-at-height employees often face. By advocating for the use of ANSI-rated equipment, OSHA ensures a uniform and nationally accepted benchmark for safety.
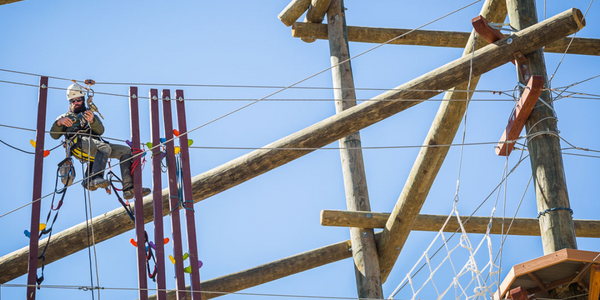
Understanding OSHA requirements for ANSI-rated equipment is paramount for professionals working in the aerial adventure industry. Here are the top things to know about ANSI equipment:
- Mandatory Use of ANSI-Rated Equipment: OSHA requires the use of ANSI-rated equipment for certain tasks within the aerial adventure industry, especially where fall hazards or other potential risks are present. This means workers must be equipped with gear that meets or exceeds ANSI standards.
- Regular Equipment Inspection: OSHA mandates that all safety equipment, including ANSI-rated gear, undergo regular and thorough inspections. This ensures that the equipment remains in optimal working condition and free from any wear, tear, or defects that might compromise its performance.
- Training & Proper Usage: OSHA's regulations aren't just about having the right equipment; they also emphasize its proper use. Workers must receive comprehensive training on how to use ANSI-rated equipment correctly. This includes understanding weight limits, proper fitting, and other specifics related to certain types of gear.
- Replacement Standards: If any piece of ANSI-rated equipment is found to be deficient, damaged, or has been involved in a fall incident, OSHA requires its immediate removal from service. The gear should be appropriately repaired (if applicable and safe) or replaced before being used again.
- Documentation & Record Keeping: Employers in the aerial adventure industry must maintain meticulous records of equipment purchases, inspections, training sessions, and incident reports. OSHA may require these records during inspections to ensure compliance with ANSI equipment standards.
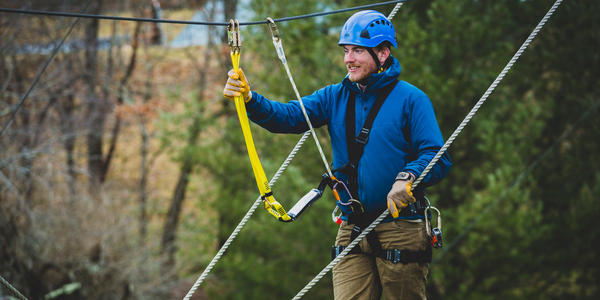
Beyond Safety
Beyond the obvious safety benefits, OSHA's requirement has legal and financial ramifications. Many regions have strict regulations and standards for work-at-height operations. By mandating the use of ANSI-rated equipment, OSHA creates a clear structure for accountability. Employers found not providing ANSI-rated equipment where necessary can face hefty fines, legal actions, and increased insurance premiums. Non-compliant businesses may also be required to halt operations until they meet the required standards, resulting in significant revenue loss.